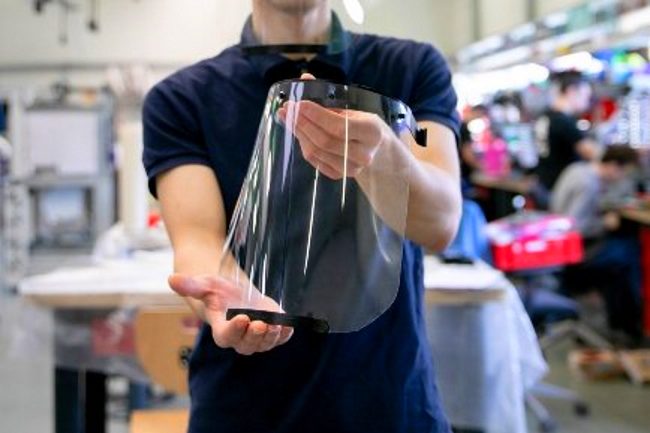
Аддитивные технологии, или 3D-печать, в течение многих лет выступали не более чем вспомогательным звеном в самых разных производственных процессах, в большинстве которых центральную роль играло другое оборудование. Но с приходом в нашу жизнь пандемии COVID-19 3D-индустрия, особенно технология FDM (FFF), смогла оперативно переключиться cо вспомогательного уровня на самостоятельное серийное производство. В первую очередь речь идет об изготовлении необходимых защитных аксессуаров для медицинского персонала, работающего в «красных» зонах.
От прототипов к конечным деталям
Индустрия 3D-печати существует уже несколько десятилетий, ее история зародилась в 1970 годах. И всё это время основной целью 3D-принтеров было создание прототипов. Это одна из задач 3D-печати в том числе и на сегодняшний день. Компании из самых разных отраслей ежедневно создают с помощью 3D-принтеров сотни различных прототипов конечных деталей, устройств и механизмов, совершенствуют их, устраняют ошибки и дефекты. Благодаря тому, что прототипирование идет внутри собственного производства и с использованием собственных материалов, это значительно ускоряет и удешевляет весь производственный процесс по сравнению с тем, если бы прототипы заказывались у сторонних поставщиков.
Однако диапазон применения 3D-печати в последние несколько лет значительно расширился и уже не ограничивается только лишь созданием прототипов. Многие компании, особенно из сфер автомобилестроения и машиностроения, постепенно переключаются от 3D-печати прототипов к 3D-печати конечных деталей, осуществляя ее прямо на своём производстве. Например, они печатают новые детали на замену изношенных для своих сборочных линий. Один из главных плюсов такого подхода — независимость от внешних поставщиков деталей. Эту технологию уже внедрили на своих производствах такие гиганты как Opel и Electrolux.
Ещё одно преимущество использования 3D-печати в производственном цикле — возможность создания кастомизированных продуктов под каждого уникального клиента. И это, в первую очередь, представляет ценность для автопрома. Например, покупатель Mini Cooper от концерна BMW может получить автомобиль с неповторимыми деталями интерьера, напечатанными специально для него на 3D-принтере.
Масштабирование 3D-производства в период COVID-19
Тем не менее, описанные выше ситуации — это всё ещё мелкосерийное или даже единичное производство. И, скорее всего, 3D-печать так бы и оставалась в этих рамках, если бы не пандемия COVID-19. В это непростое время многие производственные компании, которые раньше не были знакомы с 3D-печатью, обратили своё внимание на эту технологию, поскольку она, в отличие от традиционного производства, позволяет создавать аксессуары любой формы и размера в кратчайшие сроки. Необходимые детали для защитного медицинского инвентаря начали печатать на 3D-принтерах, причем делали это в режиме 24/7, так как спрос со стороны медицинских учреждений был колоссальный. Благодаря этому фактору 3D-принтеры успешно преодолели ступень от единичного/мелкосерийного к крупносерийному производству.
Своим опытом в этом направлении делится 3DGence — один из ведущих европейских производителей профессиональных и промышленных 3D-принтеров, работающих по технологии FDM (FFF).
Компания начала производить защитные щитки (экраны) для лица из прозрачного полипропилена, используя свой собственный парк оборудования. 32 профессиональных принтера 3DGence DOUBLE P255 были оптимизированы под серийное производство деталей для щитков. Ключевым фактором успеха была оптимизация машинного кода, которая позволила каждому принтеру произвести 3D-модель необходимого уровня качества за минимальный период времени. В результате данной оптимизации специалисты 3DGence смогли печатать одновременно по 2 элемента конструкции щитка на каждом принтере. На данную операцию требовалось 25 минут.
В трудные и непредсказуемые времена, такие как период пандемии COVID-19, ключевую роль играет гибкость любого бизнеса или производства, то есть способность адаптироваться к новым условиям в максимально сжатые сроки. 3D-печать — великолепный пример такой гибкости. Столкнувшись с огромным спросом на персональное защитное оборудование, мы разработали прототип защитного щитка для медработников и в течение двух дней напечатали на 3D-принтере все элементы, необходимые для сборки изделия. Затем мы отдали прототип в больницу для тестирования. В ходе теста мы проанализировали все комментарии от медиков и внесли необходимые коррективы в наш прототип. После чего мы приступили к массовому производству. Весь процесс от запроса до старта массового производства защитных щитков занял у нас всего 5 дней, что недостижимо для традиционного производства — Adam Przepolski, глава отдела услуг 3D-печати компании 3DGence
Запустив массовое производство защитных щитков, команда отдела услуг 3DGence за две недели работы в 2 смены смогла произвести 12000 рабочих изделий, которые были распространены по 111 медицинским учреждениям.
ООО «Туссон-Принт» является официальным представителем компании 3DGence в Беларуси. Будем рады проконсультировать вас по 3D-принтерам 3DGence. Обращайтесь по тел: +375 29 110-23-55, +375 17 389-77-34, +375 17 389-77-88.